Industrial Cooling
We offer quality solutions for cold storage and industrial cooling systems.
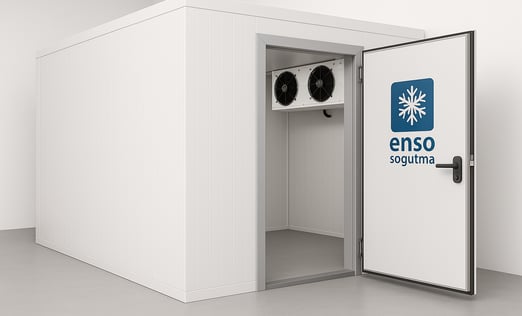
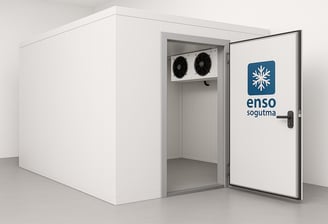
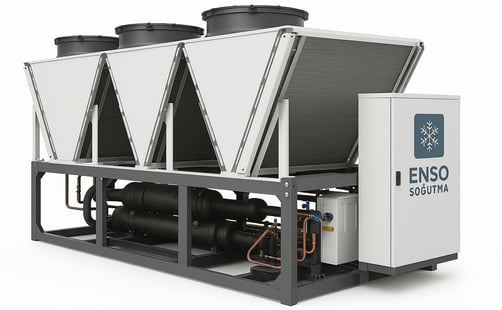
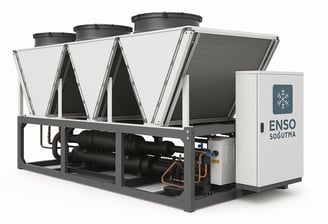
Modular cold storage systems are modern storage units that offer fast and flexible solutions for the changing needs of different industries. Here are 5 key pieces of information you should know about these systems:
Flexible Installation and Expandability: Modular cold rooms are constructed by assembling pre-fabricated standard panels. Thanks to this structure, they can be easily dismantled and moved to another location when needed, or expanded by adding new panels to increase storage capacity. This flexibility provides a significant operational advantage to businesses.
High Energy Efficiency: Modular panels, typically made from high-density polyurethane or similar insulation materials, offer excellent thermal insulation. This minimizes the amount of energy required to maintain a constant internal temperature, resulting in significant energy savings and reduced operating costs.
Fast and Easy Assembly: The process of joining standard panels using interlocking or cam-lock systems significantly speeds up the installation of modular cold rooms. They can be made ready for use much faster than traditional structures, making them ideal for urgent storage needs.
Diverse Application Areas: Modular cold storage systems have a wide range of uses, from the food industry to the pharmaceutical sector, chemical industry, logistics, and retail. Their ability to operate at different temperature ranges (chiller rooms, freezer rooms) provides suitable storage conditions for various product types.
Hygienic and Durable Construction: The smooth and easy-to-clean surfaces of the modular panels make them ideal for industries such as food and pharmaceuticals, where high hygiene standards are required. Their construction from durable materials also offers a long-lasting storage solution.
Chiller Units Cooling Systems
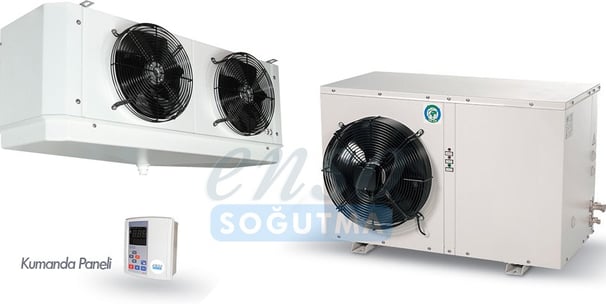
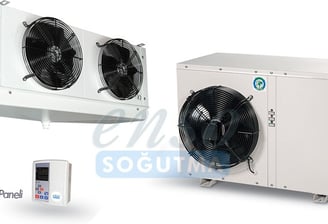
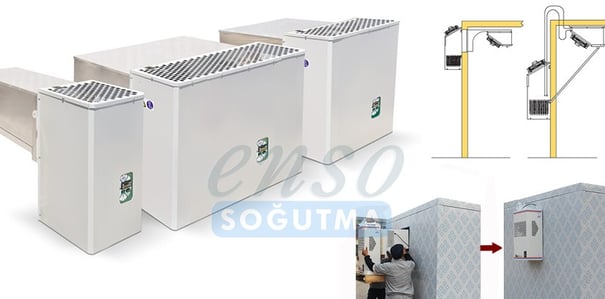
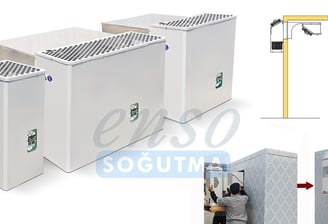
Monoblock Cooling Systems
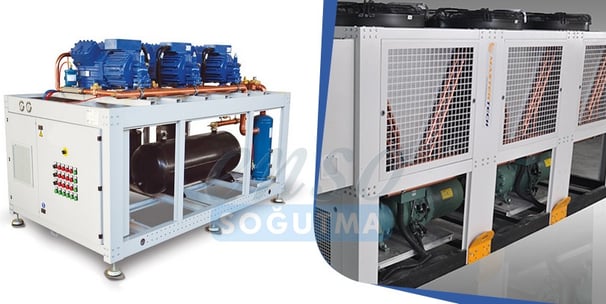
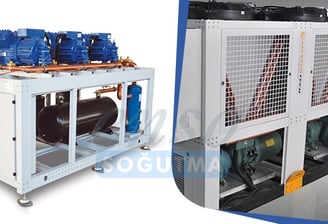
Central Cooling Systems
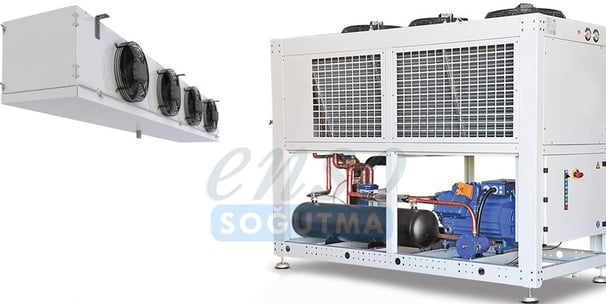
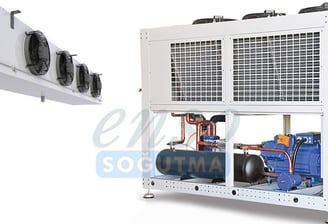
Industrial Cooling Systems
Modular Cold Room Systems
Split Type Cooling Systems
CONTACT US
Chiller units are central cooling systems widely used in industrial and commercial applications where large volumes or specific processes require cooling. Here are 5 key pieces of information you should know about chiller systems:
Provide Centralized Cooling: Chiller units cool water or a glycol solution and distribute it through piping to various points such as fan coil units, air handling units, or process equipment. This centralized structure allows efficient cooling of multiple areas or pieces of equipment with a single unit.
Available in Different Types: Chiller systems are primarily divided into two main types: Air-Cooled Chillers and Water-Cooled Chillers. Air-cooled chillers reject heat directly to the ambient air, while water-cooled chillers remove heat through a cooling tower or another water source. The correct type is selected based on the application area and available resources.
Offer a Wide Capacity Range: Chiller units are manufactured in a wide range of capacities to meet diverse cooling needs, from small commercial buildings to large industrial facilities. This variety ensures that a suitable solution can be found for the specific requirements of each project.
Energy Efficiency and Control: Modern chiller systems are equipped with advanced control systems and features like variable speed compressors to optimize energy consumption. This helps reduce operating costs as well as minimize environmental impact. The system can adjust its capacity according to the cooling demand.
Versatile Application Areas: Chiller units are used in many different fields, including comfort cooling (office buildings, hotels, shopping malls), industrial process cooling (plastic injection, metalworking, chemical industry), food processing and storage, pharmaceutical production, and data centers. They can provide precise temperature control as needed.
Monoblock cooling systems are practical units designed for cold rooms or freezers, where all cooling components (compressor, condenser, evaporator, control panel, etc.) are combined within a single compact housing. Here are 5 key pieces of information you should know about monoblock systems:
Compact and Integrated Design: Monoblock units house all the main parts necessary for the refrigeration cycle in a single block. This integrated design does not require external piping or separate units, which greatly simplifies and speeds up installation.
Easy Installation and Minimal Space Requirement: Thanks to their compact structure, monoblock systems can be easily mounted on the panel or wall of the cold room. They save space by eliminating the need for a separate outdoor unit or machine room. Installation typically requires minimal technical knowledge.
Ideal for Small and Medium-Sized Rooms: Monoblock cooling systems are generally preferred for smaller or medium-sized cold rooms and freezers. They are commonly used in places like supermarkets, restaurants, hotels, patisseries, and small storage areas.
Plug-and-Play Convenience: Many monoblock models come fully charged and tested from the factory. This "plug-and-play" feature reduces on-site installation time and complexity, allowing for quick commissioning.
Cost-Effective Solution: Due to their integrated design, fewer components, and simpler installation processes, monoblock systems generally have a lower initial cost compared to split-type cooling systems. This makes them a budget-friendly option.
Split type cooling systems, as the name suggests, are cooling solutions consisting of two main units: the evaporator unit located in the indoor environment to be cooled, and the condenser (outdoor) unit located in the outdoor environment. This split structure offers various advantages. Here are 5 key pieces of information you should know about split type systems:
Split Unit Structure: The most distinctive feature of split systems is that the refrigeration cycle takes place in two separate units. The evaporator absorbs heat from the inside, while the condenser rejects this heat to the outside. This design allows noisy components (such as the compressor and condenser fan) to be located outdoors, resulting in quieter operation indoors.
Less Heat Load Indoors: The location of main heat-generating components like the compressor and condenser in the outdoor unit prevents additional heat load from being generated within the cooled area. This increases cooling efficiency.
Flexible Installation Options: Thanks to the connecting pipes between the indoor and outdoor units, split systems offer more flexibility regarding the location of the outdoor unit. The outdoor unit can be mounted on the roof, ground, or wall, while the indoor unit is placed inside the area to be cooled.
Suitable for Medium to Large Scale Applications: Split type systems generally have higher cooling capacities compared to monoblock systems and are therefore more suitable for larger cold rooms, industrial areas, or commercial buildings. Multiple indoor units can be connected to a single outdoor unit as needed.
Allows for Longer Piping Distances: The length of the connecting pipes between the indoor and outdoor units can cover greater distances compared to monoblock systems. This provides more freedom in positioning the outdoor unit and facilitates system design.
Industrial cooling systems are complex engineering solutions designed to maintain specific temperatures or cool substances in manufacturing processes, storage, and large-scale commercial applications. These systems are typically larger in capacity, more robust, and often more customized compared to commercial and residential cooling systems. Here are 5 key pieces of information you should know about industrial cooling systems:
High Capacity and Reliability: Industrial cooling systems are typically designed to cool very large volumes or processes with high heat loads. High reliability and durability are paramount due to the requirement for continuous operation. They are usually designed to run 24/7, and redundant systems may be used in critical applications.
Diverse Application Areas: These systems play a critical role in a wide variety of industrial sectors, including food and beverage production, pharmaceuticals and chemical industries, petrochemicals, power plants, data centers, automotive, and metal processing. They are used for various purposes such as product storage, cooling process fluids, or maintaining equipment operating temperatures.
Require Customized Solutions: Industrial cooling needs vary greatly depending on the sector and application. Therefore, industrial cooling systems are usually specifically designed and manufactured according to the project's specific requirements (temperature range, capacity, space constraints, energy efficiency goals, etc.), rather than being standard off-the-shelf products.
Energy Efficiency and Environmental Impact: Energy efficiency is a critical factor in industrial cooling systems, which can have significant energy consumption. Modern systems aim to minimize energy consumption and environmental footprint by utilizing advanced control algorithms, efficient compressors, heat recovery systems, and environmentally friendly refrigerants.
Need for Comprehensive Engineering and Service: The design, installation, and maintenance of industrial cooling systems require expertise. Proper sizing, installation, and regular maintenance of the systems are vital for optimal performance, longevity, and energy efficiency. Therefore, strong engineering support and after-sales services are of great importance.
Central cooling systems are systems where numerous different areas, such as large buildings, campuses, or industrial facilities, are cooled from a single central point. These systems offer significant advantages in terms of efficiency and ease of management. Here are 5 key pieces of information you should know about central cooling systems:
Management from a Single Center: In central cooling systems, cooling energy (typically chilled water) is produced at a single central point (e.g., a chiller room) and distributed through a piping network to all units requiring cooling (fan coil units, air handling units, etc.). This structure allows the entire system to be monitored, controlled, and managed from one location.
High Capacity and Scalability: These systems have high capacities capable of meeting the cooling needs of areas spanning hundreds or even thousands of square meters, or multiple buildings. Capacity can be increased by adding extra chiller units or distribution equipment as needed, making them ideal for large-scale projects.
Energy Efficiency Advantages: Using larger and more efficient central chillers instead of multiple smaller cooling units generally provides higher overall energy efficiency. Furthermore, energy consumption can be optimized with technologies like variable flow pumps and advanced control systems. Additional systems like heat recovery can also be integrated.
Reduced Noise Pollution: Concentrating noisy compressor and condenser units in a central area significantly reduces the noise level in the cooled living or working spaces. This is important for comfort, especially in places like hotels, office buildings, and residential complexes.
Easier Maintenance and Service: Having all major cooling equipment in a central location simplifies maintenance and service procedures. Service personnel only need to focus on one point instead of being dispersed throughout the building or facility. This makes maintenance processes more efficient and cost-effective.
ENSO SOĞUTMA
We specialize in industrial cooling systems.
info@ensosogutma.com.tr
+90 532 615 1021
© 2024. All rights reserved.